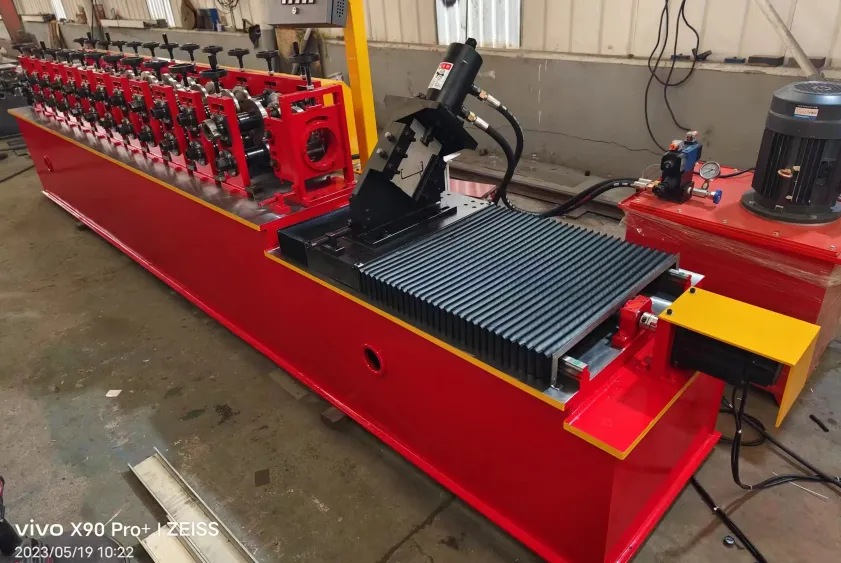
Drywall Light Keel Roll Forming Machine – the ultimate solution for efficient and precise drywall construction. Designed for modern manufacturing needs, this state-of-the-art machine revolutionizes the way drywall keels are produced, ensuring high-quality output with minimal labor and time investment.
Our Drywall Light Keel Roll Forming Machine is engineered to create lightweight steel keels that are essential for drywall installation. With its advanced roll forming technology, this machine can produce keels in various sizes and specifications, catering to diverse construction requirements. The robust design ensures durability and longevity, making it a reliable addition to your production line.
Drawings
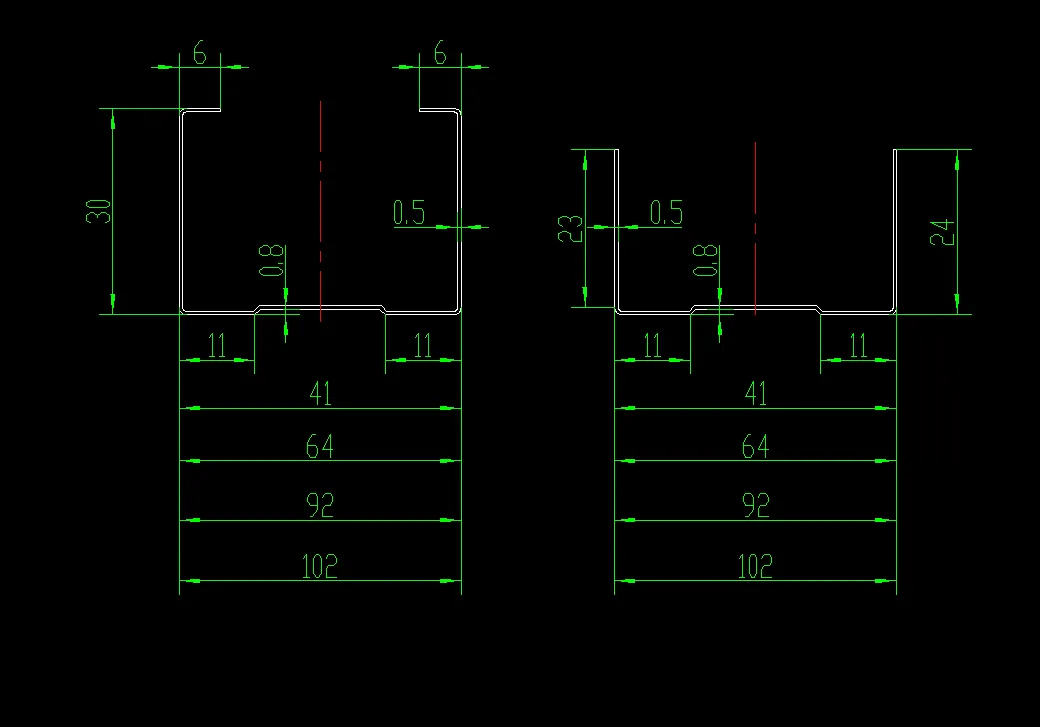
Processes and components
Manuel decoiler |
x 1 set |
Guiding machine |
x 1 set |
Main roll forming machine |
x 4 set |
Servo tracking cutting system |
x 4 set |
Hydraulic station |
x 1 set |
PLC Control system |
x 1 set |
Run-out table (3M*2) |
x 1 set |
Working Process
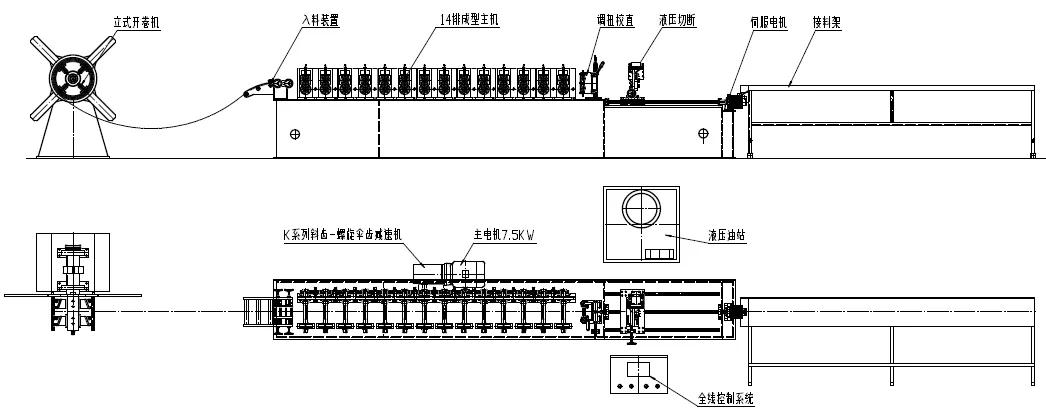
Decoiler
1) Capacity: 3 tons
2). Manual decoiler
|
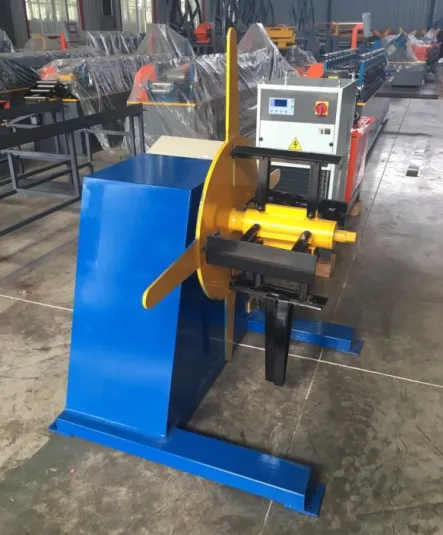 |
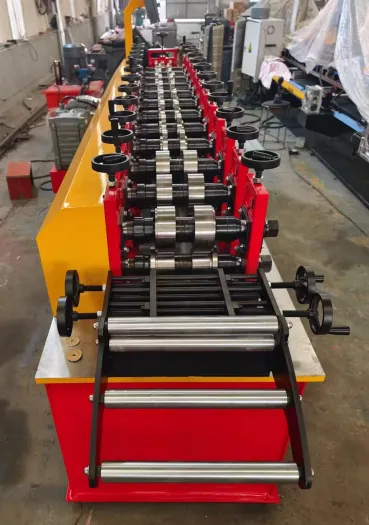 |
Material guiding
Input width adjustable
|
Roll forming machine
Matching material: Galvanized or PPGI
Material thickness range: 0.3-0.9mm
Forming speed: 0-40m/min
4. Main power: 5kw,
Hydraulic station:4.0kw
5. Quantity of roller:10
6. Shaft Material and diameter: ¢50mmmaterial is 45CR
7.The way of driving:Gear
8. Controlling system: PLC
9. Voltage: 380V/ 3phase/ 60 HZ
10.Material of forming rollers: Cr12,HRC58-62
11.Material of cutter blade: Cr12 mould steel with quenched treatment,HRC 58-62℃
12.Hydraulic servo track cutting
|
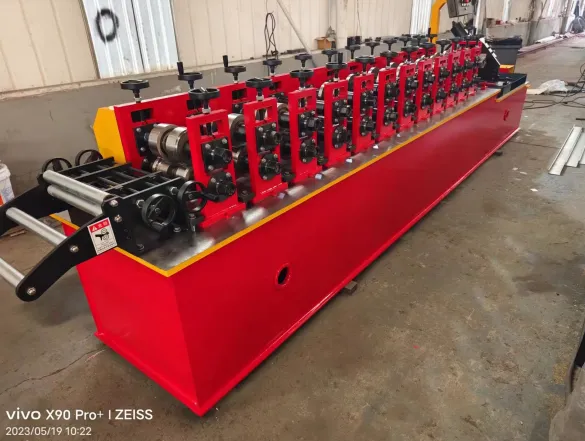 |
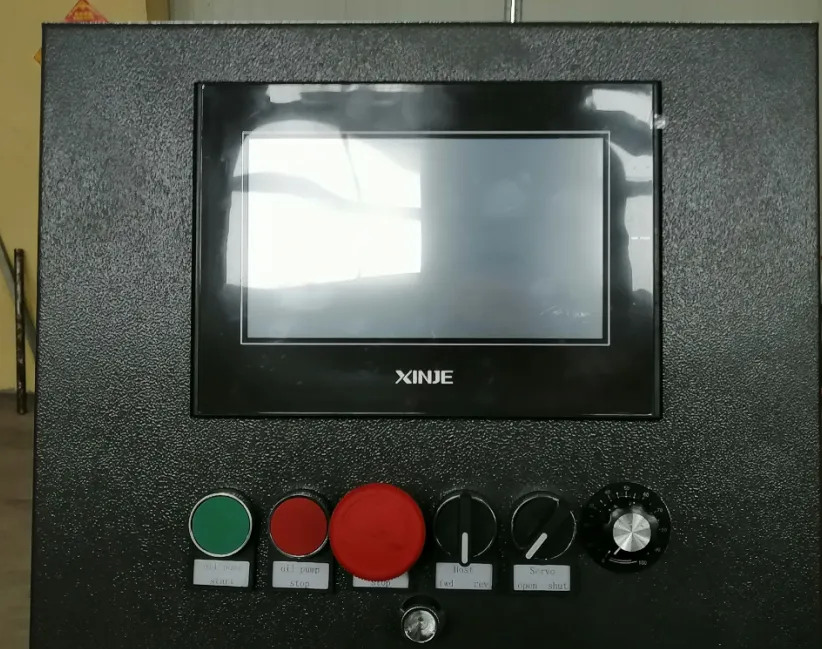 |
Control system
It adopts PLC to control. The target piece’s length is adjustable and digit of it can be adjusted. Computed mode has two modes: automatic and manual one. The system is easy to operate and use.
|
Hydraulic station
Motor power of hydraulic station: the power is 7.5Kw, and the hydraulic station drives the cutting system
|
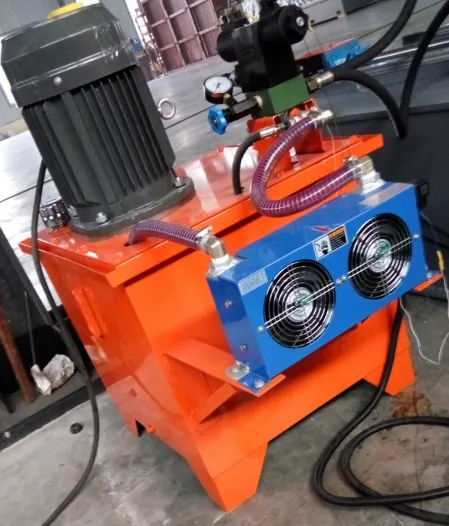 |
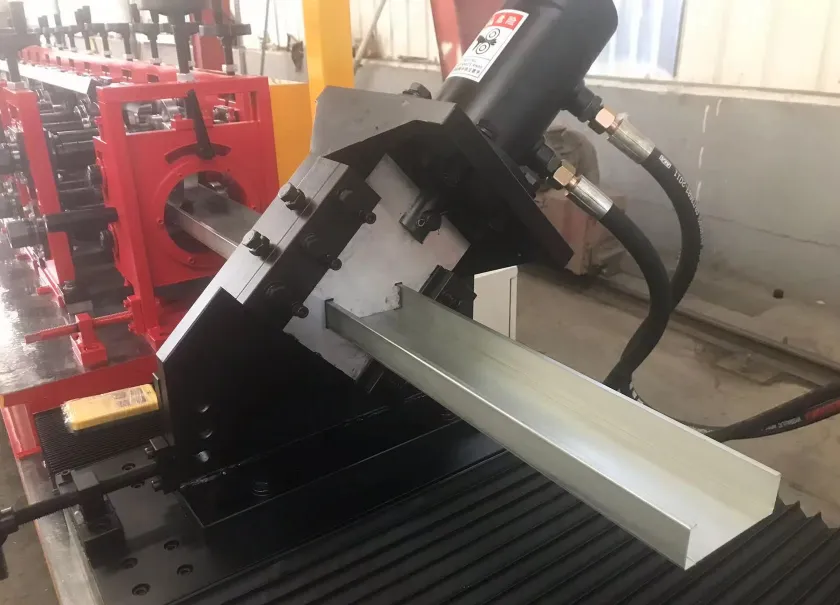 |
Servo track cutting system
1.Tolerance of length: +/- 1.5mm
2.Material of blade: CR12 with heat treatment
3.Length measuring: Automatic length measuring
4.Control: by setting on the PLC system
|