- Manuel decoiler
- Uncoiler: passive unwinding, manual tightening
- Load-bearing capacity of uncoiler: 5T
- Inner diameter of uncoiling machine: φ508mm
- Rolling range: φ460-530mm
- Rolling width: ≤500
-
|
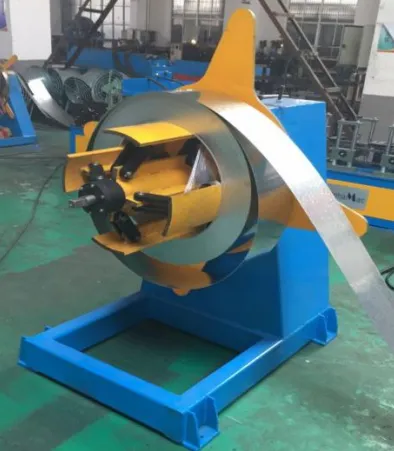 |
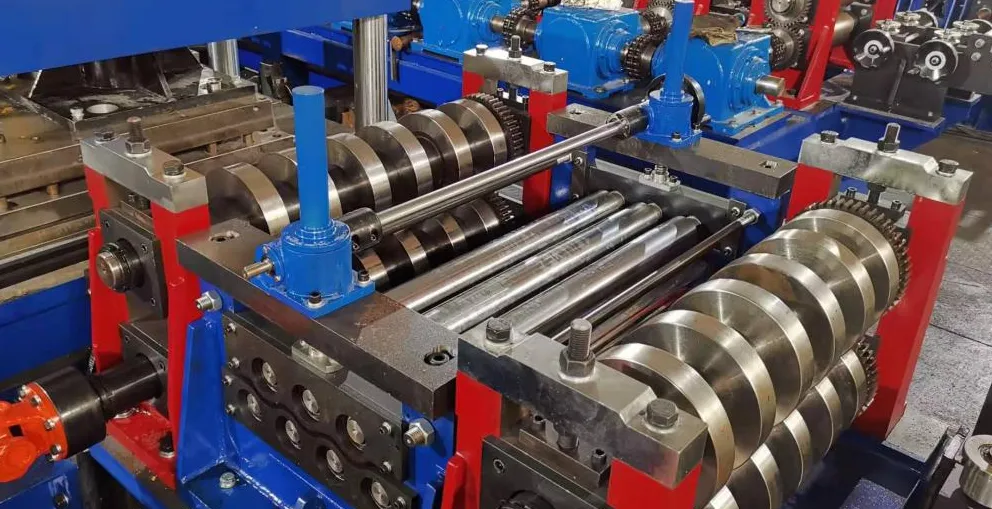 |
- Feeding system
- 1.Guided feeding :When the lateral roller type main machine feed inlet is provided with left and right guides, the two sides of the raw material plate enter the main machine after being guided from the left and the right, so that the raw material plate and the roll forming system maintain the correct position. The guide position can be adjusted by the manual screw mechanism, and the left and right are independently adjustable. The guide roll is quenched.
-
- Leveling mechanism structure: front and rear double rollers pinch, seven rollers leveling
- Diameter of leveling shaft: Φ80 (Harbin Bearing)
4.Material of leveling shaft: 40Cr quenched and tempered (HB220-260)
5.Surface treatment method of leveling shaft: super-finishing after high-frequency quenching, hard chromium plating treatment
6.The method of adjusting the gap between the upper and lower rollers: turbine elevator adjustment
-
|
Hydraulic punching system
1.Punching mechanism structure: four-column hydraulic punching (the punching frame steel plate is tempered after welding)
2.Punching die: 1 pair
3.Material of upper and lower die of punching die: SKD11 (HRC58-62)
4.Material of upper and lower templates: high-quality carbon steel after quenching and tempering, super-finishing processing
|
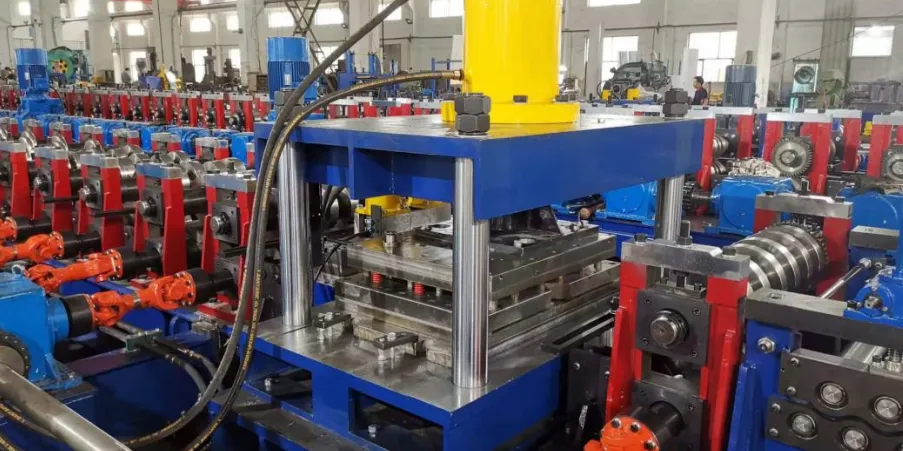 |
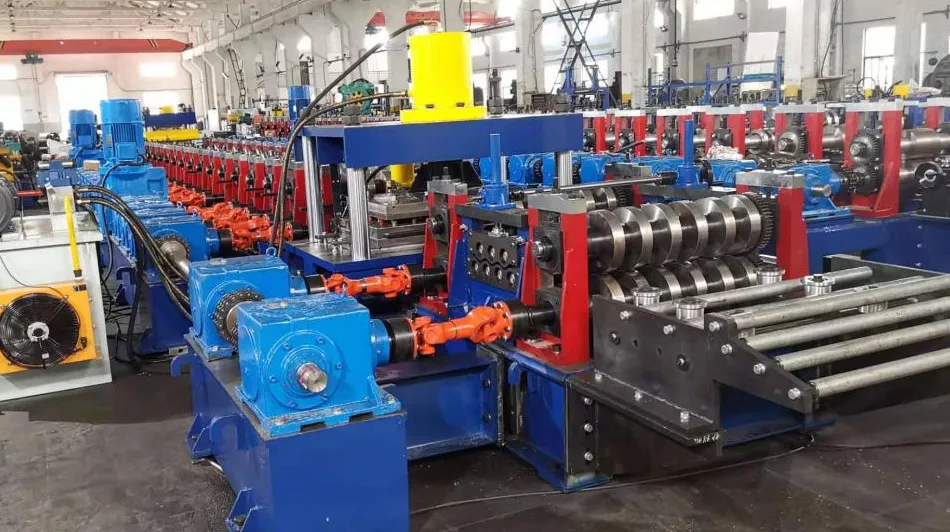 |
Roll forming machine
- Matching material: according to the drawing
- Material thickness range: 3mm
- Main motor power:30kw
- Forming speed: 0-15m/min(include the punching)
- 5. Quantity of stands: about 12
6.Material of forming rollers: Gcr15
- Shaft Material and diameter: ¢80mm,
material :40Cr quenching and tempering treatment (HB220-260)
8.Tolerance: 3m+-1.5mm
9.Controlling system: PLC
- 10. Voltage: 220V/ 3phase/ 60 Hz
- 11. Roll heat treatment method: quenching treatment (HRC58-62)
- 12. Roll mold processing method: CNC lathe processing
13.Forming machine structure: cast iron archway gearbox transmission
14.Gear box model: GY230 type gear box
|
Hydraulic cutting
1.Cutting method: hydraulic cutting after forming
2.Shear blade material: Cr12mov quenching treatment (HRC58-62)
- 3.Hydraulic station power: 22KW
4.Hydraulic station structure: two circuits
- 5.Hydraulic station oil pump: plunger pump
6.Solenoid valve: Beijing Huade (24V safety voltage)
7.Cooling method of hydraulic system: air cooling
|
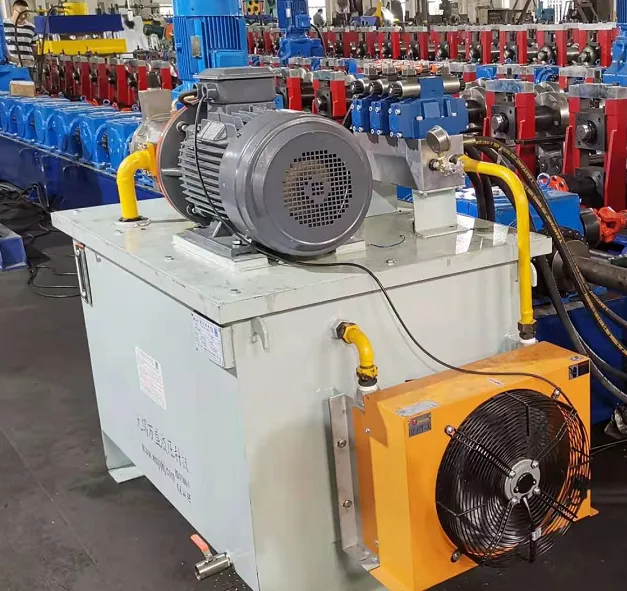 |
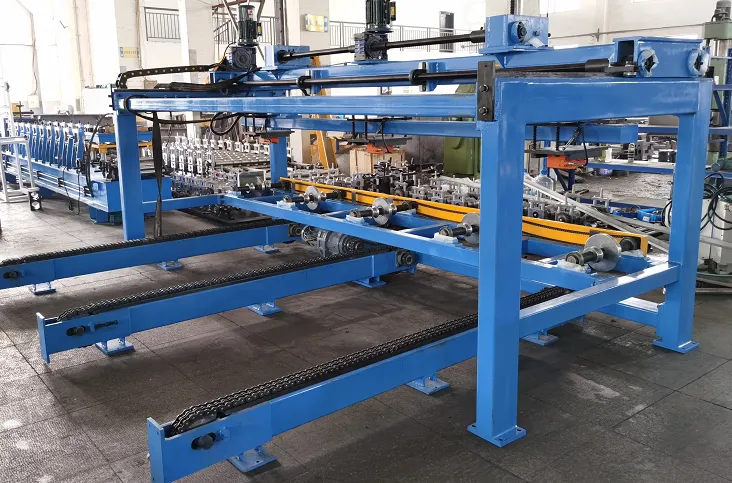 |
- Automatic stacker
-
1.Stacker length: 4.3 meters
2.The main structure of the stacker: square tube welding, with roller sliding
3.Lifting motor power: 3KW
4.Traverse motor: 1.5KW
5.Cylinder swing blanking
6.Electrical control system: the main electrical components adopt well-known brands
|
- Control system
-
1.Inverter: Yaskawa (Japan)
2.The computer adopts PLC control: Panasonic
3.Computer operation panel: MCGS
- Encoder: Koyo
5.Voltage: 220V/ 3phase/ 60 Hz
6.Other electrical components: all use domestic well-known brands
|
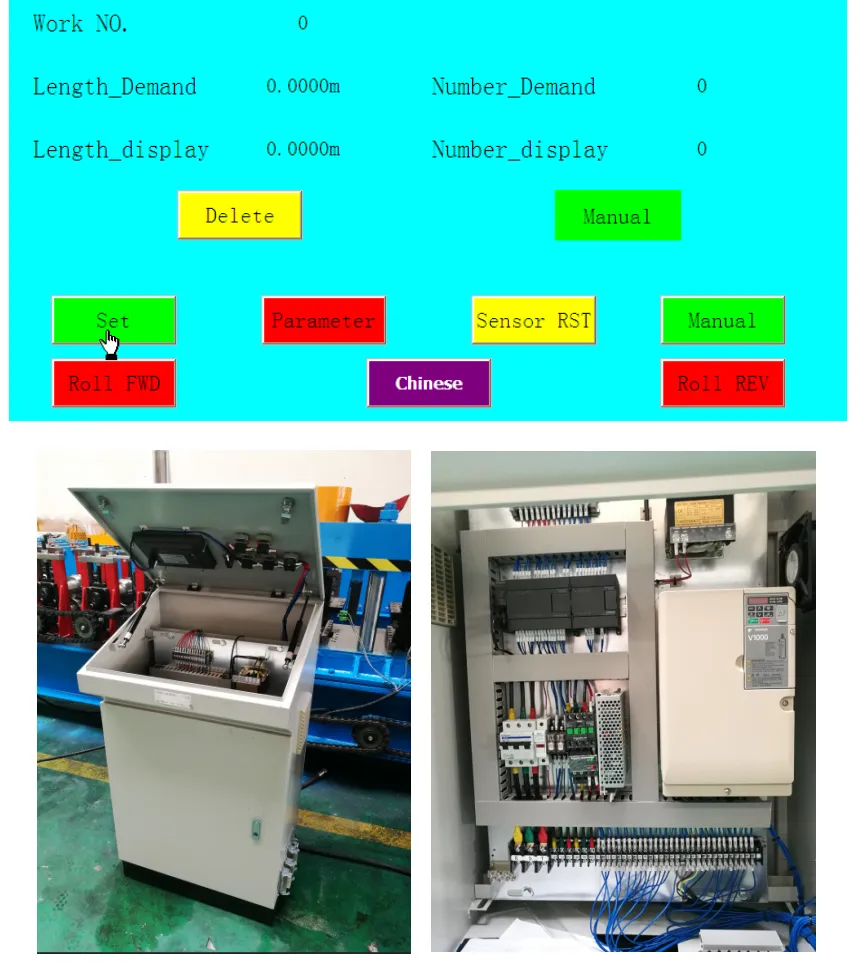 |